CAMPOFRIO turns to ULMA for its drainage system again
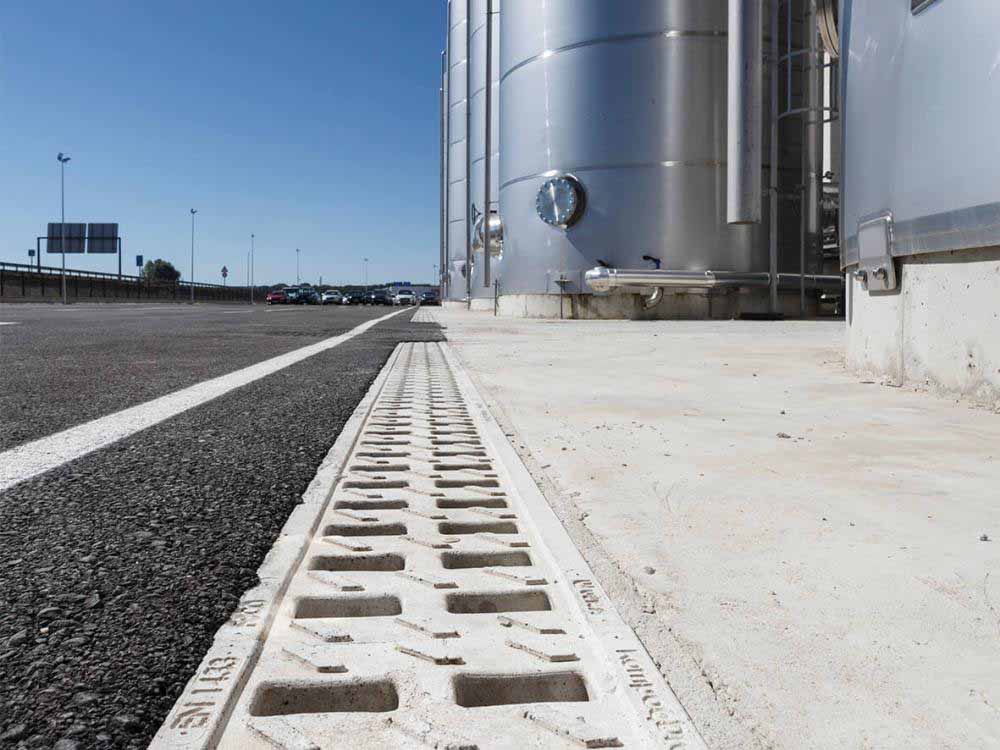
With an investment of 225 Million Euros, a surface of 99,000 m2 and a production capacity of more than 100,000 tonnes a year, CAMPOFRÍO’s new plant in Burgos, which recently reopened after a fire devastated the old installations 2 years ago, is the largest and most modern meat complex in all of Europe.
ULMA Architectural Solutions participated in this project by supplying the stainless steel drainage system, incorporating products designed specially to ensure the highest levels of hygiene for the industry.
In total, more than 1,000 lineal metres of stainless steel channels and grooved channels with the Hygienic Pro ® grills and more than 400 stainless steel drains of different types were installed, along with watertight manholes. ULMA’s stainless steel drainage system is specially designed to remove the organic remains that accumulate during industrial meat processes, permitting quick cleaning and guaranteeing excellent antibacterial performance. The Hygienic Pro ® Grill has an approved special design that facilitates cleaning.
Campofrío already contracted ULMA for the construction of the stainless steel drainage system in its pizza factory in Soria some years ago, with such positive results that the promoters were keen to use the product again in their Burgos plant; a very high-quality, easy and quick-to-clean product that guarantees the highest levels of hygiene and durability, while fulfilling all the requirements and regulations demanded in the sector.
Apart from the internal stainless steel drainage system, ULMA also supplied 300 lineal metres of the exterior KOMPAQDRAIN® drainage channel. This new compact channel is manufactured in polymer concrete: the channel and the grill form a single piece, guaranteeing greater resistance and rigidity. Thanks to its innovative MAX FLOW® system, which uses a curved design at the opening where the water enters, the speed is much faster, naturally creating a “self-cleaning” effect, while increasing the drainage capacity.
The Phoenix rises from its ashes: reopening the new factory in just 2 years
The company started its “Phoenix” Project, after the fire devastated the old factory in Burgos, which employed 1,000 workers, committing to rebuilding and reopening the plant exactly two years after the disaster.
This demanding timeframe represented a significant challenge for the works, meaning materials had to be supplied immediately and based on the needs that arose, in coordination with the engineers and the owners.
Thanks to the efforts of the company, the institutions and the employees and unions, the factory reopened in record time, on 23 November 2016, with 318 employees; it is now working at full capacity again.